Cold Saw Machinery
Cold saw system refers to a system that uses a rotating blade of high speed steel (HSS) or (Tungsten carbide tipped) TCT to perform the cutting operation, in which case the heat from cutting to the chips The chipping operation is shifted and as a result the blade and the cut piece remain cold. This is exactly the opposite of the situation that occurs in systems based on friction and friction (Friction Saw) and the result is the creation of a lot of heat and a paste solution in the part and the result of the cutting operation.
In the overhead system, the cutting force is transmitted to the blade by a reduction mechanism and increasing torque. This is usually done by a gearbox that is connected to an electric motor controlled by an inverter system with constant torque.
The blade is advanced when cutting by another motor that has a constant torque and by a mechanism that has a looseness of almost “zero. The propulsion motor is usually of the” Permanent Magnet “type with its own controller.
During cold cutting, the amount of chipping per unit time is relatively high and no pleats or discoloration of the part and groove is produced during cutting.
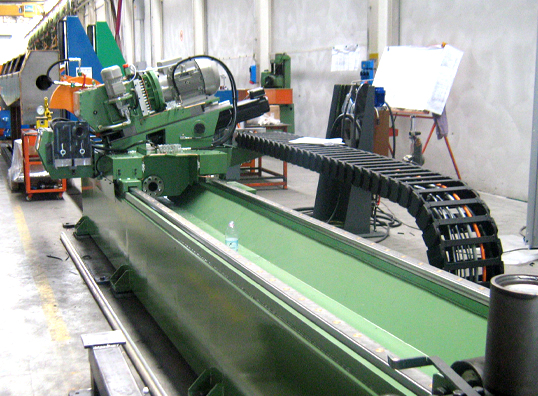
Another point is that due to the high torque of the blade when cutting the desired piece must be held in place by a rigid support system. Any looseness or looseness of the mechanism produces abnormal sound and vibration and eventually breaks the blade.
In cold cutting, the number and size of teeth and the rotation speed of the blade are very important according to the type of cutting section, the material of the piece and the advancing speed. This information is provided by the saw blade manufacturer in special tables.
Cold cutting tools have been used in a wide range of cuts around the world for many years. The increasing quality of these products has enabled them to be a leader in metal cutting. In this regard, first the structure and raw materials as well as heat treatment of such blades should be identified and then the types of blades and other technical specifications and cutting process should be explained in detail …
Raw materials
Soap water blades (cold bars) are made of Super HSS steels and are manufactured by ISO 9000 certified companies. This guarantees the quality of the products produced, in which case the declaration of the steel number and details of the analysis by the manufacturer is mandatory.
For example, the analysis of the steels used is as follows
It is a super HSS steel with a high percentage of tungsten and molybdenum. After heat treatment, this steel has a high hardness with sufficient toughness. A certain amount of tungsten in the composition is required to form a very hard and wear-resistant carbide to reduce the wear of the production tool under working conditions. Tungsten also increases the mechanical strength of the tool, increases its shear efficiency and prevents austenite grains from coagulating. Molybdenum is the main element that ensures the formation of the fine structure of martensite and in addition maintains its stability and mechanical properties. Vanadium is also the element that forms the hardest alloy carbides in the structure of steels and prevents the growth of austenite grains and increases the toughness.
This is a super HSS steel that, in addition to the alloying elements in 1.3343 steel, has about 5% cobalt. Cobalt does not form carbide, but in HSS steel it stabilizes the structure at tempering, prevents grain growth, and yet maintains hardness at high working temperatures. These characteristics are very important when cutting very high alloy steels such as stainless steels as well as very hard metals that cause high temperatures in the cutting area.
This steel is prepared using powder metallurgy technology. This technology has made it possible to obtain a steel whose stress is reduced to a minimum due to its layering and has a very high uniformity and there is a minimum risk of micro-cracks in it. These properties of steel reduce the deceleration speed of the cutting edges and increase the hardness and cause high toughness.
Heat treatment
Proper and constant heat treatment to achieve a full efficiency of materials and technological properties of HSS steels is a principle and confirms and completes all technical specifications of products. Operation furnaces
The heaters have modern computer equipment that controls the hardening and tempering process steadily and precisely, thus guaranteeing the highest quality standards and the stability of the blades. Metallurgical laboratories check the results of the process on a daily basis, thus ensuring the highest quality standards.
In this process, the disc or the raw blade is automatically guided into the furnace and heated to 1200 degrees Celsius and then quickly to a temperature of 60 degrees Celsius, under a set of presses that prevent it from changing shape. It is cooled and finally, after heat treatment, the manufacturing processes are completed.
Surface coatings
The coatings are carefully designed for each specific cut. Surface coating units, to machines that use the latest available technologies to create PVD coatings. It has been Equipped . Nano-coating machines have made it possible to deposit more molecules per unit area, thereby increasingly improving both adhesion and wear resistance of the coating. These coatings are unique and are the result of ongoing theoretical research in the field of machinery and materials in universities and the practical application of applications with the guidance of machinery manufacturers and their consumers. This is a joint effort
In practice, this has allowed the blades to be coated with a layer of nano-strips containing components of noble chemical elements (titanium, aluminum, chromium and zirconium).
Covers
To achieve the best possible performance, the coating is important to ensure that the work surface is in the best condition in accordance with the highest standards and that the blade surface is sufficiently prepared to achieve the best adhesion. Appropriate methods have been considered to achieve the results. These methods depend on the surface condition to be covered. The surface roughness should be RZ 0.3 and a washing phase should be performed on the surface with chemical stimuli and then vacuum drying. The method of washing and drying creates surface products that are completely “dry and clean” without any oxidation, which in practice gives the best possible adhesion to the seated layers.
It guarantees. The surface coverage, the amount of warping and the bowl of all the blades are checked and if they are found to be out of tolerance, they are separated.
Technical characteristics of coatings
To show the main technical characteristics of coatings, some of the results of studies conducted by research teams are presented in the form of diagrams.
This coating is formed at a process temperature of about 490 ° C. This coating has a coefficient of friction of 0.47 and an oxidation temperature of 640 ° C. Layer hardness
Covered reaches 2480 Vickers (HV 0.05). Its low thermal conductivity provides thermal protection for the substrates. This coating is suitable for cutting low-alloy steels and must use lubricating oil when cutting. This coating is not suitable for cutting copper, brass, and bronze.
This coating is made of titanium and carbon plasma, which increases the hardness up to 3000 Vickers. The coefficient of friction of this layer is reduced to 0.22 due to the presence of carbon in it. This makes this coating very suitable for cutting highly abrasive materials such as stainless steel and medium alloy steels with a maximum strength of 800. Low coefficient of friction reduces the amount of pleats at the cutting edge. This coating has an oxidation temperature of 400 ° C and lubricating oils must be used when cutting with it.
This coating is obtained from a combination of titanium, carbon and steel gas plasma. This coating has a very low coefficient of friction of 0.18 and its hardness reaches about 3200 Vickers. These two characteristics not only cause excellent shear by reducing the coefficient of friction but also increase the quality of the shear surface. This coating has an oxidation temperature of about 470 ° C, so lubricating oils must be used when using it. This type of coating is especially suitable for cutting stainless steels, titanium, hard steels, as well as copper and brass.
In this coating, plasma is obtained by melting the titanium / aluminum cathode. The addition of a neutral gas during the process and the applied energy that directs the molecules to the surface to be bombarded create a layer with excellent properties that ensures high thermal resistance of the substrate. The oxidation temperature of this layer is about 800 ° C and its hardness reaches 3400 Vickers. The coefficient of friction of 0.45 makes it suitable for excellent cutting, especially in limited lubrication conditions. This type of coating is especially suitable for cutting high-alloy steels up to a strength of 1100 N / m2, cutting cast iron, stainless steel and all materials that produce high heat during cutting.
This coating has been prepared by a research team in collaboration with the metallurgy unit of a university. They created special conditions for the cathode and the resulting plasma. This coating provides protection against abrasion of the hard layer by creating a layer of solid lubricant on the surface. This lubricant causes better flow of chips created in the cutting groove and prevents the chips from sticking to the surface and makes the chips easier to dispose of. This coating has an oxidation temperature of 880 ° C and its coefficient of friction is 0.55 and its surface hardness reaches 3500 Vickers. These conditions make it possible to achieve better results under harsh cutting conditions and to cut very hard materials under low lubricant conditions. This coating is recommended for cutting stainless steel with a strength of 100 Newtons per square millimeter, aluminum and inconel.
Round saw blade executive tolerances
Executive tolerances for the production of circular saw blades are derived from the 1840 Dean standard.
Technical Specifications
In the following section, the amount of conic as well as the amount of warp of the blades produced by the soapy water are presented.
The teeth of the soapy water blades are machined using CNC machines and CBN stones. The roughness of the created surface is very small and it causes better removal of chips from the teeth and also prevents the chips from sticking inside the teeth. In addition, for each specific application, a special type of tooth is designed, which is described below.
Choosing the right tooth and cutting angle is very important to get the best results from the saw blade. This choice depends on the material and the cross section you want to cut.
To choose the right number of teeth, it is very important to consider the section to be cut and its material. Basically, the toothed step is correct when in solid materials the ratio of the tooth to the cross section is at least 1: 3 and in cutting the profile and pipe cross section this ratio is 1: 1.
The following recommended angles are suitable for specific applications.
Technical specifications of production blades
In order to obtain the correct cutting parameters for each specific application, a series of issues must be considered. The factors such as (materials, machine, tools, etc.) directly determine the results. Calculate blade and load.
When the material and cross section were determined. The toothed step must be selected. Choosing the right tooth step prevents dangerous vibrations and ensures the removal of chips. The following data are approximate.
In order to get the best work of the blade, its sharpness is also very important. Therefore, it is recommended to use only CNC machines that have lubricants and CBN stone to sharpen the blades. Accuracy in creating free angles and chipping is very important and the tooth must have full curvature and correct depth.
In collaboration with a company that produces abrasive stones, a stone has been made that is specifically designed for re-sharpening and indenting soap blades. The CBN material and its resin bond create teeth with excellent polishing quality while maintaining the geometric shape of the stone. These types of stones are specially designed for use on CNC machines such as Schmidt, Loroch, Bozinaro, Soko and Kenta machines. To produce suitable tools, it is recommended to always use soap or cutting oils. When working with these types of stones, speed The circumference should be between 30 and 50 meters per second and the cutting depth should be 0.03 to 0.1 mm.
Recommended working parameters
In the following section, the recommended working parameters in the field of cutting speed and fruiting when cutting solid materials, pipes and profiles are presented.
Formulas and cutting examples
The following formulas can be used to determine the saw cutting speed, the number of blade revolutions per minute and the yield. Using these formulas completes the data presented in the previous table.
The number of blade revolutions, indicated by rpm and meaning the number of blade revolutions per minute, can be measured using a telemeter. The blade circumference is obtained by knowing the ambient velocity of the following formula.
Determine the amount of loading
Loading speed, expressed in millimeters per minute, is the speed at which the blade travels into the workpiece. Loading is directly related to cutting time and decreases with increasing loading speed.
Shear velocity (circumferential) in meters per minute = vt
Load rate per tooth in millimeters per tooth = Avz
Blade diameter in millimeters = D
Number of teeth = Z
Loading or feeding speed in millimeters per minute = Av
Number of blade revolutions per minute = RPM
Examples for calculating cutting parameters
For cutting solid rebar with a diameter of 30 mm, we have NCD4 38 steel with a strength of 1000 MPa with a blade with a diameter of 350 mm.
According to the table we have.
The choice of tool depends on what the user wants to achieve. Reducing cutting time is not always the goal. Other factors such as the quality of the cutting surface, the life of the blade and ……… are also considered.
Practical example 1
Cutting material: 304 stainless steel with Mpa800 strength
Pipe cutting section with a diameter of 85 and a thickness of 2 mm
Cutting cost in terms of machine cost per hour Euro / h 50 is equal to Euro / min 0.83
Practical example 2
Cutting material: S235 steel with Mpa450 strength
The cutting cross section of the can is 30 x 70 and the thickness is 2.5 mm
Cutting cost in terms of machine cost per hour Euro 50 is equal to Euro / min 0.83
Practical example 3
Cutting material: 37 SMN PB steel with 500 Mpa strength
Solid round cutting section with a diameter of 37 mm
Cutting cost in terms of machine cost per hour Euro / h 50 equivalent to Euro / min 0.83
Cutting time of each piece = t Yield = Av Number of revolutions = Rpm Cutting speed = Vt
Cutting cost per piece = C Time per piece = S Total time = T Number of cutting heads = N
General cutting problems and solutions
Various factors affect the cut. Sometimes we think that everything depends only on the part being cut and the tools used. Detailed studies of the cutting process show that other factors are effective in the cutting process, the most important of which are the quality of the saw blade, the quality of the material to be cut, the correct gripping of the workpiece, the amount and quality of lubricant used, the stability of the machine used for cutting. , Fruiting speed control, sharpening quality, etc.
Sometimes the problem with cutting is a combination of several factors mentioned above, so it is difficult to find the problem. In the following section, we describe some of the problems that we encounter during cutting along with the solution to solve it.
Failure of soap blades is usually due to hooking at work, impact to the blade due to rapid impact. The blade with the workpiece at the beginning of cutting, loosening the blade or workpiece and the workpiece leaving the clamp during cutting.
If the blade has been sharpened several times before failure, the failure of the blade has nothing to do with its production and one of the above can be the reason for the failure of the blade.
If the blade breaks in the same few primary cutting heads, it is likely that the blade is due to production processes. In this case, the blade must be checked by the experts of the manufacturer and find the cause.
The reason for the slowing of the blades is usually due to the hardness of the blades or the misuse of the blades. Soap blades are usually produced and marketed with a hardness of 62 to 65 Rockwell C. If the blade hardness is less than 62 Rockwell, the blade does not have the required efficiency and slows down quickly. Improper use slows down the blades, such as cutting hard material, cutting thick and thick materials, using inappropriate cutting speeds, or cutting off the flow of coolants.
Soap water blades are provided with a maximum twist of 0.2 mm and a maximum of 0.1 mm. Usually, the defects of the cutting machine increase the warping and lameness of the blades.
As mentioned before, the standard blades offered in the market are only for cutting profiles and solid iron and aluminum sections, and if these blades are used to cut other materials, there may be problems in cutting, in which case the recommendation It is possible to consult with the experts of the manufacturer.
Dean standard for saw blades
Production blades for pipe cutting are also made of HSS DMO5 steel or HSS-CO5 steel and are suitable for portable carriage machines. These blades are produced with BW toothed type for cutting pipes with a thickness of 3 to 5 mm. HSS-CO5 steel is used to produce blades for cutting stainless steel.
Select the tooth form
To increase the productivity of the tool, it is very important to choose the right tooth form. Choosing the right tooth form ensures the removal of chips and reduces shear stresses and prevents the blade and workpiece from heating up during cutting.
Toothed form A
This form of indentation is usually used for the industries of jewelry production, grooving of screws with very fine indentations, as well as in other industries according to DIN-1837 A standard.
Toothed form B
This toothed form is usually used to cut very thin sections of pipes and profiles at times when it is not necessary to break the shavings to remove the shavings.
Toothed form C
The C or HZ toothed form is usually used to cut rods and solid sections. This toothed form consists of a forward tooth with two sides chamfered and a final incisor that has no chamfer. Its height is between 0.2 to 0.3 mm more than other teeth.
Toothed form BW
This indentation form is commonly used for thick pipes and profiles. In the BW indentation form, the indentations are chamfered uniformly between left and right.
Friction shear blades (fire)
Friction blades are mainly used to cut all types of pipes and construction profiles from St37 to St52, which have a strength of 600-300 Mpa. These blades are made of 1.2235 and 1.26604 steel. Unlike cold blades, this The blades cut at very high speeds. These blades first raise the cutting point temperature when cutting and start cutting when the condition of the cut piece enters the plastic area. No coolant should be used when cutting. And to increase the life of the blade, it is better to cool the blade after the operation by using a suitable coolant.
These blades are heat-treated using precision equipment and their hardness after tempering can reach between HRC 46-42, depending on the hardness of the material to be cut. Since this type of blade works at a very high speed and generates a lot of heat when cutting, this type of blade must have very precise dimensional tolerances and have a suitable tension level to prevent twisting and hooking during work. Therefore, it is recommended for the stability and optimal quality of friction blades, it is better to observe the following ratio between the diameter and thickness of the blades.
It is better to choose between 5 to a maximum of 8 mm for cutting, depending on the thickness of the piece to be cut. If the thickness of the profile is less than 5 mm, the toothed step between 5 and 6 is suitable, and if the thickness of the profile is more than 5 mm, the toothed step of 7 to 8 is suitable.
The working parameters of friction blades are largely influenced by the plastic conditions of the material being cut.
Unlike cold blades, where the payload per tooth can be defined, such a definition cannot be given for friction blades (fire). In this case, only the amount of material released per unit time can be expressed. In this case, the amount of 200-500 mm2 / sec can be considered.
The toothed form suitable for fire blades for cutting carbon steels at a temperature of less than 100 ° C is similar to the figure below. The cutting angle of these blades should be between zero and minus 3 degrees.
Causing fire blade problems
Standard fire blades are usually produced with a diameter of 520 and a number of 300 teeth with a hardness of 1 RHRC ۵ 45. The ideal cutting speed with these blades is 3500 to 4500 rpm. Problems that are sometimes justified by consumers. be . as follows :
Usually, incorrect use of the blade, such as cutting at higher or lower speeds than standard, cutting thick and thick materials, using cooling materials when cutting, etc., will cause the blade to slow down quickly. The issue can be investigated if the blade is slowed down at the appropriate speed when cutting the iron profile
(Low blade stiffness causes it to slow down more)
Various factors that cause fire blades to crack are:
Weak electric motor and reduced blade speed when cutting
Use coolant when cutting
Cut thick sections and stick the blade in the workpiece
Cut with slow blades and apply double pressure to the blade
Improper sharpening of the blade
Contact of the workpiece with the blade surface due to lateral pressure during cutting which causes intense heat to be applied to the blade.
Due to all these issues, if the blade has cracked abnormally before the first sharpening and if the teeth have not yet slowed down, the cause of the crack can be investigated.
For information, it is quite common to create 2 to 3 shallow cracks after a period of operation for fire blades
This is perfectly normal, given the frictional function of the blades, which are cut by friction.
Swing and limp
The allowable warp of 520 blades is about 0.3 mm and their allowable crank is 0.15 mm. This problem can be corrected if the amount of warping and lameness of the blade is more than the mentioned range. However, as mentioned in the case of soapy blades, “usually the problems of the cutting machine increase the warping and lameness of the blades. These problems are:
The flanges or pleats used, the shafts of the machine are twisted, the bushing is broken, etc. Therefore, the above items should be checked before using the blades.
If double pressure is applied to the blade during cutting or the workpiece is involved with the blade, this will cause the blade to overheat and the blade tension will be disturbed and the blade may move away from the flange over time